SUSTAINABILITY
SUSTAINABLE AGITATORS
FIT FOR THE FUTURE
MUT-Tschamber is a leader in the development and service of sustainable agitators. Our process chain begins with our innovative configurator, which is directly linked to a specially developed CFD simulation. This performs the first optimization cycles and transfers the results directly into our Digital Twin. From this system, which we feed with data from Condition Monitoring, we generate behavioral models based on a generic approach. This enables us to calculate fault scenarios and thus make valid statements for Predictive Maintenance.
SIGNIFICANT INNOVATIONS
OPTIMIZED AGITATOR TECHNOLOGY AND PREDICTIVE MAINTENANCE
Together with a university, we have developed a configurator that is directly linked to a specially developed CFD simulation. In view of the wide range of possible applications and the different requirements placed on agitators, it is crucial to find the right configuration for the respective area of application. This is where our configurator comes into action. It enables the development of customized solutions for specific requirements, defining the optimal settings and specifications for the agitator that meets the customer’s individual needs. This reduces the risk of miscalculations that could lead to inefficient processes or even damage to the equipment.
Thanks to the precise calculation and quick design of the agitator, the configurator helps to reduce costs. The optimized selection of components means that only the materials and sizes actually required are used. This avoids oversizing, which could not only result in higher acquisition costs, but also higher operating costs. The configurator also reduces the need for expensive prototypes and test runs, as the digital design already provides a very accurate forecast of the agitator’s performance.
The use of our configurator supports our efforts to create sustainable agitator solutions – sustainable agitators.
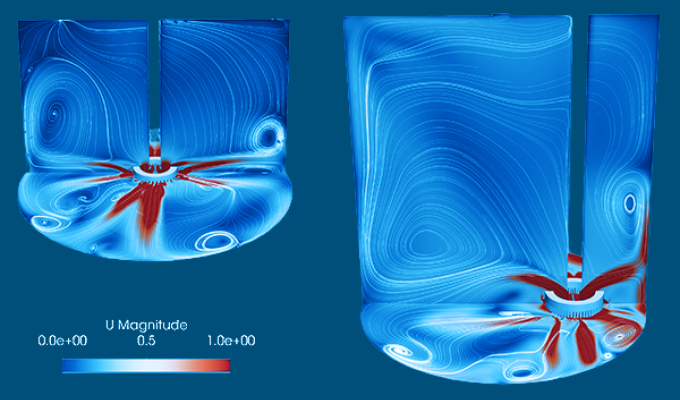
SUSTAINABLE AGITATORS
THE MUT-TSCHAMBER PLATFORM OF THE DIGITAL TWIN
The optimized data from our CFD simulation is transferred directly to our Digital Twin platform – a key to optimization and innovation. We can map, simulate and optimize real processes in a virtual environment. Our system is fed with data from Condition Monitoring. In this way, we generate behavioral models with well-founded statements for Predictive Maintenance and greater operational reliability.
Signs of wear and potential problems can be detected at an early stage, the service life of the machines can be extended and greater operational reliability is guaranteed. Not only maintenance costs are minimized, but also any unplanned downtimes.
With our approach, consisting of configurator, flow simulation and Digital Twin, we support the flexibility and adaptability of our customers. Processes can be optimized, costs reduced and innovations driven forward. This strengthens competitiveness in the long term. Our contribution: sustainable agitators.
ENERGY EFFICIENCY FIRST AND FOREMOST
AGITATOR COMPARISON
ENERGY EFFICIENCY FIRST
COMPUTATIONAL FLUID DYNAMICS
ENERGY EFFICIENCY FIRST